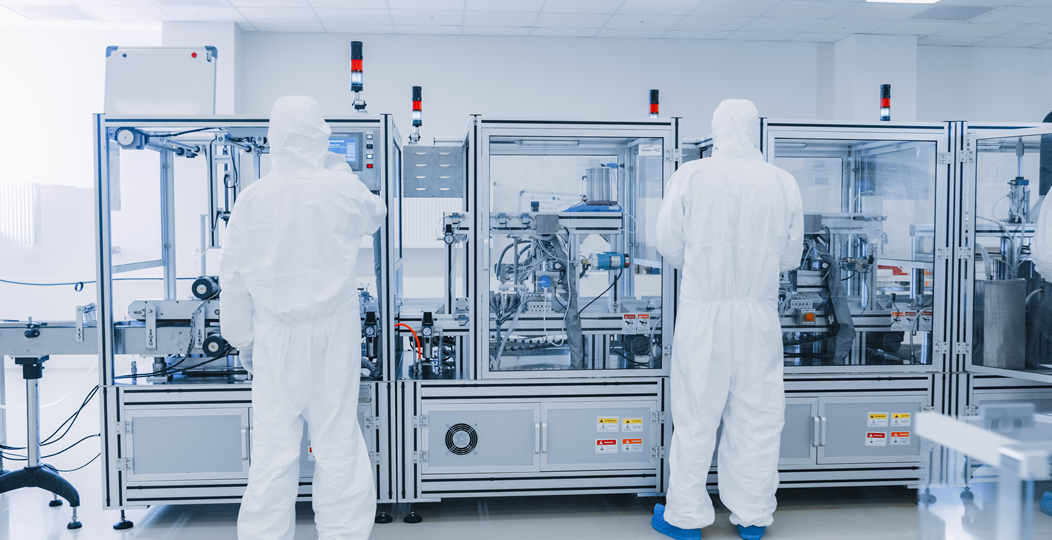
Laser additive manufacturing has evolved over several decades and is today capable of printing products to the highest specifications in terms of both form and material resilience. How then can optimising the specification and handling of the optical components such as both optical chamber windows and debris shields make a difference?
As technology and business practices advance, the ethos of continuous improvement demands increased efficiencies in terms of improved quality, lower cost and faster processing from laser additive manufacturing, also known as 3D printing, systems. In this context optimising the precision optical component technology can be a game changer and has the potential to create significant competitive advantage. Simple improvements in the fabrication of the optics and then on-site handling can make big differences.
The Manufacturing Challenge
Our customer uses additive manufacturing equipment to fabricate products for the aerospace industry and confronted a persistent challenge that was systematically undermining their manufacturing precision. The area of weakness in their system was the processing chamber windows – crucial optical components positioned directly above the build platform with the purpose of protecting the laser and other parts of the system but allowing for laser beam transmission.
These precision windows operate in an extremely demanding environment. During each manufacturing cycle, microscopic amounts of vapourised alloy particulates combine to create a thin, absorptive film on the window surface
The resulting contamination layer progressively disrupts laser transmission, preventing lasing consistency and introducing significant variability into the manufacturing process.
The performance is limited by:
- Constant material contamination.
- Reduced laser energy transmission.
- Potential thermal degradation of optical surfaces.
Existing Approach and its Limitations
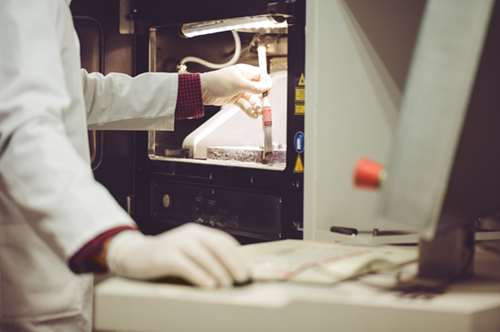
When we visited our customer’s facility, we found that machine operators were using inappropriate cleaning methods to remove the contamination from the optical chamber windows. Whilst suitable for use in other processes they were less than ideal for working with optical components. The fact is that these methods inadvertently caused more harm than any benefit that might have been gained from their use. Typical practices involved the use of off-the-shelf dry cloths and brushes, applied with inconsistent techniques. These risked surface scratching and reintroducing contamination.
The cleaning process became a cycle of degradation. Each cleaning attempt effectively caused further damage to the windows, reducing product lifespan and compromising manufacturing precision. Furthermore, the variability in operator technique meant that no two cleaning processes were identical, thus introducing an unfortunate element of uncontrolled variability to the operation.
Our Comprehensive Solution
Our intervention addressed both the cleaning methodology and the optical component design through a holistic engineering approach.
Optical component enhancement
Additive manufacturing components at scale can be a dirty business with optics under stress from contamination damage and thermal stress. Unlike prototyping laboratories, the continual repetition of the process with a high output of parts printed means a considerable amount of contaminant produced. The challenge was to provide optical components capable of withstanding the harsh environment of the inside of a laser additive manufacturing system, providing greater transmissivity over longer periods of time between being cleaned and repeated manual cleaning. Working directly with our customer’s R&D engineers, we developed a more resilient optical coating with higher laser damage threshold (LDT) based on ion-assisted deposition (IAD) technology. This provided more robust chamber windows and debris shields. The result was:
- Harder coatings for the internal window surfaces.
- Improved durability against cleaning processes.
- Enhanced resistance to thermal and contamination stress.
Cleaning protocol innovation
We recommended a specialist cleaning method based on our optical handling experience over decades. The new approach used disposable optical-grade cleaning wipes with an alcohol-based solution, implemented as a strict wipe-and-discard methodology. This eliminated the risk of re-contamination and significantly reduced surface damage potential. The result was:
- A cleaning process which cleaned the optics rather than making them more dirty.
- Contaminant was removed with minimal damage (scratching) of the optics.
- The optical chamber windows had a longer lifetime before needing to be replaced.
Measurable Outcomes
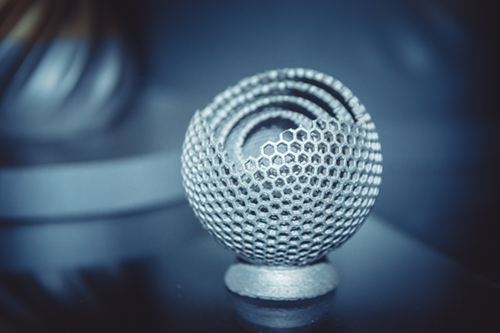
The collaborative solution delivered significant improvements in the system performance. Extended optical component lifetime translated directly into more consistency in laser energy transmission and a reduction in manufacturing process variability.
Critically, our customer was able to achieve significant cost savings by:
- Reducing component replacement frequency.
- Lowering overall operational costs.
- Purchasing directly from MPO.
The collaborative approach also opened possibilities for recycling and reworking of the optics, thus introducing both economic and environmental benefits.
MPO’s Distinctive Approach
Our philosophy extends beyond simple component supply. We partner with customers to understand their specific challenges, developing tailored solutions that address real-world manufacturing constraints. We recognise that though the science maybe the same, lasers used for different applications in industry, medicine and scientific research need a different approach to the supply of optical components.
The core of our approach combines deep technical expertise with a commitment to practical problem-solving. By focusing on value-driven engineering solutions, we help customers – in this instance manufacturers – realise new levels of precision and efficiency.
Contact us to find out more about optical windows for 3d printing and additive manufacturing.