At MPO we specialise in the design and manufacture of larger optics for high energy laser systems. We have decades of experience in fabricating low surface roughness large optics, high laser-induced damage threshold (LIDT), for a reasonable price, under one roof.
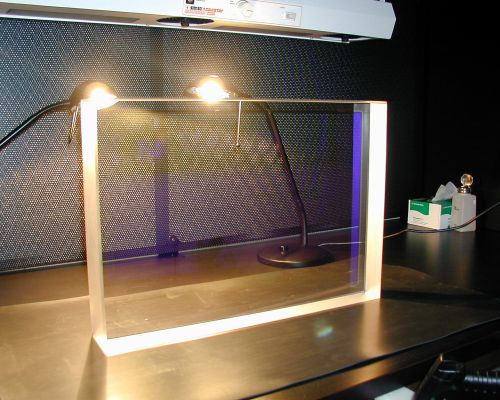
We know that our customers are developing ever more powerful laser systems and that high energy lasers require large optics to be able to expand the beam. We are experts in producing large (up to 500mm), planar and spherical optics and then coating them to meet the exacting requirements of the world’s most powerful lasers. Our streamlined manufacturing processes and in-house capabilities allow us to deliver exceptional value without compromising on quality.
LOW SURFACE ROUGHNESS
Many years of experience has enabled us to refine our optical processing. From the outset, our grinding and polishing processes have been engineered to remove subsurface damage. We use continuous polishing as opposed to CNC or magnetorheological finishing (MRF). We believe that pitch polishing processes have a much tighter control over the mid-spatial frequencies (MSF) that can have an impact in very high-powered laser systems.
Each optic is polished individually, taking in to account the thickness to surface area ratio, the coating wavelength, type and thickness and we then tailor the surface figure specifically, prior to coating, to ensure that post coating flatness is to specification.
Minimising the low surface roughness of our optics means that our customers can be confident of minimal MSF errors.
HIGH LIDT COATINGS
Here at MPO, we understand that high-power and high-energy lasers can cause significant damage to optical components due to their high power and energy levels. Large optics aren’t exempt from this. Our understanding of LIDT means we’re able to push the boundaries of the possible.
Use of appropriate deposition techniques guarantees that our coatings provide both LIDT protection and transmissivity at the relevant laser wavelength. Precise control of both the coating design and its application means that the flatness after coating can be assured, the LIDT is maximised and the optic bears minimal coating-induced stress.
METROLOGY
We have invested in metrology to enable us to measure optics over an 18”/450mm aperture. This gives superior and more accurate assessment of the overall surface figure than taking many smaller footprint image.
EXPERIENCE
We have always been R&D lead and extensive experience over time of with the world’s biggest laser systems and supplying them with large optics. We understand high energy lasers, their requirements, how they’re evolving and the needs of the engineers developing and maintaining them.
Our polishing team deploy knowledge gained over many years to polish optics according to size, aspect ratio versus shape and the planned coating. Our coating engineers each have over 20 years’ experience and in-depth knowledge of thin film design and application processes. We take great pride in understanding residual gas partial pressures, gas bleed in rates, materials, evaporation rates, temperatures and the overall process of control that links these together. We understand the precise stress levels and deformation of surface a coating can exert, even on large optics.
We are proud to work and supply large optics for the largest and highest powered lasers in UK, Europe and the USA.
All of our optics are designed, shaped and polished and coated in one facility on the Isle of Man. This enables us to set our pricing such that we offer a consultative service, delivering superb quality large optics at a reasonable price.
Our coating engineers each have over 20 years’ experience and in-depth knowledge of thin film design and application processes. We take great pride in understanding residual gas partial pressures, gas bleed in rates, materials, evaporation rates, temperatures and the overall process of control that links these together. We understand the precise stress levels and deformation of surface a coating can exert, even on large optics.