In this section, we provide an overview of the distinct initial processes an optical blank goes through before it can be coated. Raw glass must be put through multiple, distinct phases of production before satisfying the extremely high standards required for precision optics. Specifically the processes are shaping, grinding, polishing, edging and where relevant, contacting.
MPO we are equipped to carry out all steps of glass-based fabrication processes from small sample to OEM quantities.
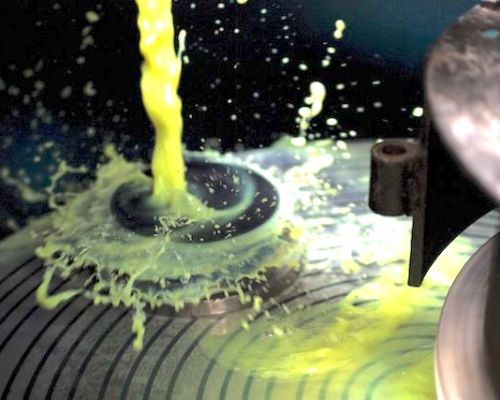
Shaping
Our products begin life as glass blanks. Being no more than a piece of material fresh from a factory, a blank is understandably very rough and will not be in the desired shape of the final optic.
The blank needs to be machined to bring its dimensions closer to that of the final piece. Plano-surfaces are machined using a surface grinder where either a single part or a large number of small parts are fixed to a rotating table and ground against a lap.
If the final piece is a lens, then the radius of curvature is ground into the optic during this step. The blank can be tailored to any desired focal length by adjusting the radius of curvature in the tooling used to grind the product.
Grinding, Polishing, Edging
With the glass now in roughly the right shape it undergoes loose abrasive lapping or grinding to remove fractures caused by shaping and improve the overall surface roughness and remove sub-surface damage. Before this can happen however, the edges of the optic are bevelled to avoid small pieces of material chipping off and scratching the surface. The lapping process removes glass via the friction between the glass and the lapping plate in conjunction with a combination of water and grit.
To manufacture extremely flat optics with high laser damage threshold, we take extreme care at each of the fabrication process. In the case of these initial stages, we carefully control our grinding process to ensure we use the correct materials and grinding grain sizes to ensure a smooth and reflective ground surface in preparation for the polishing stage.
The glass is then finely polished to the point at which the optics reach their surface finish and form. Usually this means improving the surface roughness from micrometre scale to sub nanometre and down to approx. 0.3nm or 3 angstroms.
In regard to size, we have the ability to polish and coat optics from a few microns up to approximately 500mm diameter.
We compensate polish our substrates. This means that we know exactly what stress our coatings put on to an optical component of any given size and shape. We can therefore adjust the surface flatness (figure) of the optic before coating to assure flatness after coating (without the need for any further compensating coating which can lower laser-induced damage threshold (LIDT).
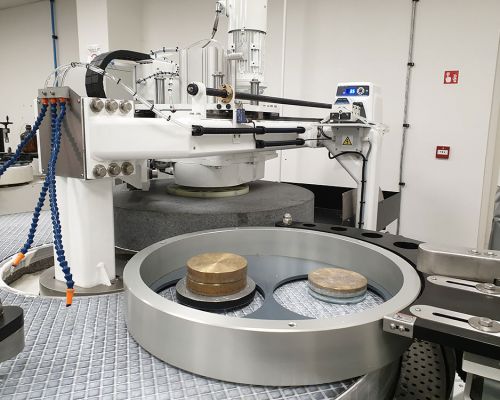
Optical Contacting
At MPO we specialise in the ability to contact coated optics to each other (in addition to uncoated parts).
This means we can make polarising cubes or complex optical assemblies for high-energy lasers without the use of adhesives or other chemical-based techniques.
Through our understanding of surface smoothness and flatness we have developed the ability to permanently contact two parts (or more) together. The two surfaces to be contacted require a specific flatness and the coatings a specific surface roughness and cleanliness in order to achieve this. The result is that we can produce polarising cubes with far higher damage thresholds than conventional cemented products.