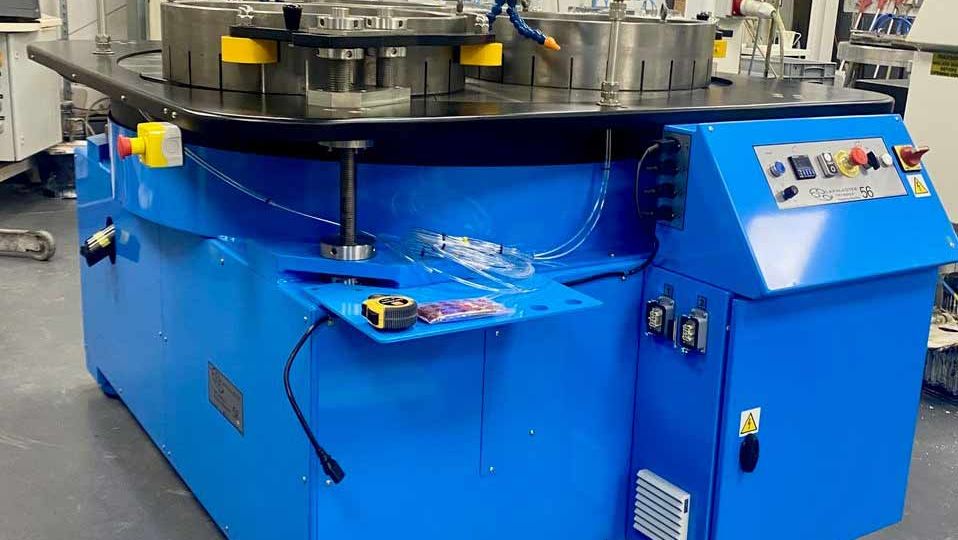
Last year we discovered that raw material blanks entering our processes didn’t meet our high standards. Before entering the MPO fabrication process, optical blanks need to meet very specific surface roughness and surface form specifications. Regrinding the sub-standard parts would have taken weeks on the equipment we had, so we had to send them back to the suppliers to reprocess.
We realised that if we took control of the process and ground our own substrates, we could control the quality and the speed of processing and so invested in a 56” grinder.
The challenge
The highest quality optics start with the highest quality raw materials. To eliminate sub surface damage on finished optics we specify rigorous ground surface finish and flatness – even on raw materials. Last year we discovered inconsistencies in the ground surface finish of materials delivered to us. Although the issues were minor, the fact is that the substrates supplied to us were slightly convex rather than completely flat. Left untreated, the optic doesn’t polish uniformly and so takes longer to process.
We had a problem. We couldn’t accept the blanks as they’d been supplied and so had to return the parts to the supplier to be reworked. This put back our production and delivery schedules at the time.
The solution
The upside to this situation however, was that we realised the gains that could be made by bringing this early part of fabrication process in-house. Our investment in a 56” grinding machine marked a pivotal moment, enabling us to grind our own substrates from a rawer form of material and so take further control over the manufacturing process.
Our new grinder completed commissioning in February of this year and means we can now control the amount of material to be removed, speed of removal and surface finish of the ground substrate. Eliminating sub surface damage and allowing a quicker and more beneficial polishing.
As a result we have an increased control of raw materials, and have expedited the grinding process, significantly compressing lead times.
Key Benefits and Impacts
Our investment in a new piece of machinery has a number of benefits for our customers. By internalising the grinding process we gain ownership of quality control and mitigate the risk of receiving non-conforming parts from suppliers. We can now achieve a higher surface quality and integrity from an earlier stage in the manufacturing process.
Our customers have benefited from our increased vertical integration. Our extended ability to quickly correct any imperfections in the surfaces of raw materials provided means we can run a tighter schedule and so provide our customers with reduced fabrication lead times.
Wrap up
We view the purchase of a large grinder as an example of continual improvement as we refine our processes and increase our capabilities. Our company mission is to set the global industry standards for high-energy laser optics in terms of quality, durability and size.
Our recent investment exemplifies this commitment. This powerful new piece of equipment allows us to ensure greater control over quality and reduce lead times. Ultimately, this translates into superior products delivered to our customers faster.
Quality, fair price and prompt delivery underpin the way we do business. The addition of the large grinder means we can better control these factors.
Read more about the initial processes we undertake in fabricating optical components here.