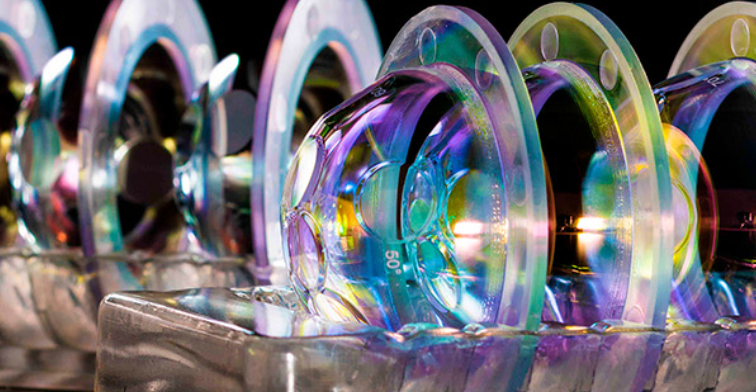
At the 10th Symposium on Optical Coatings for Laser Applications on 8 May in Vilnius, Manx Precision Optics Managing Director Dr Helmut Kessler will give a presentation exploring the change of approach needed in manufacturing large optics.
With the typical size of optical components for research applications having shown a significant increase over the last decade we take a closer look at the scalability, or lack thereof, experienced in the fabrication of large optics used in high-energy laser systems.
Lasers now measured in petawatts (one quadrillion watts) are now commonly used for high-energy research. Some researchers are planning exawatt power systems. As lasers become ever more powerful, the demands placed on optical components grow in complexity and scale. The higher the power, the greater laser damage threshold (LIDT) needed. It’s fortunate then, that to some extent this problem can be mitigated by using large optics.
What are the factors we must consider when it comes to both specifying and fabricating the large optics for high-energy laser systems?
What Counts as “Large” Optics?
Whilst there is no strict industry-wide definition, at Manx Precision Optics (MPO), we classify optics as follows:
- Small: ≤150 mm diameter
- Medium: 150–300 mm diameter
- Large: ≥300 mm diameter
These categories are driven by practical considerations-handleability, production methods, and metrology needs-not just by size alone.
Key Differences: Large vs. Small Optics
Handleability: Size and Weight Matter
As optics get larger, their weight and thickness increase dramatically. For example, a 25.4 mm fused silica optic weighs about 7gms, whereas a 500mm optic can weigh over 30 kg. This escalation impacts every stage-from safe transport and handling to installation in high-energy laser systems. Specialised equipment and procedures become essential as optics scale up in size.
Production Equipment: Scaling Up Means Rethinking Everything
Polishing
Pitch polishers range from 24” to 96” in diameter. However few manufacturers offer polishing on the very largest such machines. This is because any machine larger than 72” cannot be transported from the equipment manufacturer and so requires specialist assembly at the production site. These machines offer less commercial flexibility, incur significantly higher costs, and require longer adjustment times. The sheer size of both the equipment and the volume of materials used needed to process large optics means facilities able to accommodate such production are very rare.
Coating
Coating chambers must also scale, with sizes up to 1800 mm. Larger chambers require more powerful pumps, increased energy use, greater coating material consumption, and longer turnaround times. This reduces commercial versatility and can drive up costs.
Metrology: Measuring Quality Gets Harder
Precision metrology is critical for high-performance optics. Standard interferometer apertures (4” to 24”) are often much smaller than the optics being measured. Measuring a 500 mm optic over a small aperture can mask significant flatness errors across the full surface and best practice is to use a larger device such as the 18” (457.2mm) interferometer used at MPO. As optics grow, ensuring uniform quality and flatness across the entire aperture becomes a far greater challenge.
Why Make Optics Larger?
One of the main drivers is the need for higher laser-induced damage thresholds (LIDT). While advances in high LIDT coatings are ongoing, current technology often falls short for small optics at extreme power densities. By increasing the size of a component, the laser energy is distributed over a larger area, mitigating the risk of damage.
For example, a protected silver mirror withstands about 2.5 J/cm² in 10 ns at 1064 nm, while a dielectric mirror can handle over 35 J/cm². To match the performance, a silver mirror would need to be roughly four times the diameter of its dielectric counterpart.
How is a large optic fabricated?
Substrate Materials
High-power optics typically use materials like fused silica, BK7, and low-expansion glasses such as Corning ULE or Schott Zerodur. While LIDT is rarely a limiting factor, other considerations such as surface quality, thermal stability, homogeneity, and cost change as optics increase in size.
Coating Materials
Dielectric coatings, especially oxides, offer higher LIDT than metals due to lower absorption. Common oxides include SiO₂, Al₂O₃, HfO₂, Nb₂O₅, Ta₂O₅, and TiO₂. The choice of coating material, deposition method (e-beam, IAD, sputtering), and process parameters all play crucial roles in performance and durability.
Manufacturing Process
With large optics, the same steps are required as with smaller optics. However these steps become more complex and processing times increase:
- Substrate shaping and grinding become more demanding as size increases.
- Polishing requires larger, more precise equipment.
- Coating must ensure uniformity across a much greater surface area.
- Metrology needs to adapt to verify quality over the entire optic, not just a small section.
Laser-Induced Damage: The Critical Test
LIDT results can vary widely depending on pulse duration, beam size, and the ratio of beam to optic diameter. Heat dissipation and coating morphology are critical factors. In the femtosecond regime, LIDT is governed more by the electron band gap of the coating material, with high-index materials often being the limiting factor.
Conclusion
The shift from small to large optics is about much more than just scaling up dimensions. Every aspect-handleability, production, coating, and metrology-becomes more complex and critical to success. As high-energy laser systems continue to push boundaries, understanding and mastering these differences is essential for researchers, engineers, and manufacturers alike.
Join us at the 10th Symposium on Optical Coatings for Laser Applications to learn more about these challenges and how we here at MPO are addressing them. If you can’t make the conference, you can contact us for an informal discussion about your large optics needs.