Precision is paramount in laser optics, and even minimal dust contamination can severely impact the performance and reliability of optical components. This article provides an overview of what’s entailed in ensuring that laser optics remain dust-free throughout the manufacturing process and once delivered to the customer.
By adhering to critical best practices, you can safeguard the quality and longevity of your optical systems, ensuring optimal performance and minimising the risks of contamination.
Throughout manufacturing an optic must be frequently cleaned to ensure it is free of dust and other contaminants throughout the process. Dust contamination can affect all stages of the optical fabrication process. For example dust within the polishing process can cause scratching on the optics. Dust contamination during the coating process primarily occurs whilst the optics are being prepared for coating and can lead to inclusions in the optical coating, thereby rendering an expensive optical component worthless. Cleaning therefore takes place at multiple points during fabrication, usually before and after key processes.
It is important to keep in mind that once a product reaches a customer it should be handled with great care and kept clean to ensure optimal functionality. This is even more critical in the case of high LIDT components as even a small amount of dust can scatter laser light and drastically reduce LIDT, risking irreversible damage to the part.
MPO’s coatings come in two classifications with regards to handling and cleaning: durable and ultrahard. Generally, durable coatings correspond to some protected metal or fluoride-based coatings, and ultrahard coatings tend to be fully dielectric, but also include specific metal and metal-hybrid coatings. For a durable coating, dust should be removed from the surface by gently blowing it off with Nitrogen or other inert gas. Wiping it may damage the coated surface. An ultrahard coated surface may be wiped clean with lint free tissue, dampened with pure methanol or Isopropanol. Care should be taken, although moderate pressure may be applied when cleaning such coatings.
Cleanrooms
Any reader who has ever visited a semiconductor manufacturing plant cannot fail to be impressed by the extensive cleanroom facilities that such factories have. In general, a cleanroom can be described as an environment with a low level of pollutants, in the case of optical coating manufacture, dust particles.
Outside, under the open sky, a typical cubic metre of air contains between 30 and 40 million dust particles of 0.5mm diameter or larger. Clearly an environment is unacceptable for the manufacture of precision optics. Hence, an environment needs to be created that reduces dust contamination to a suitable level.
ISO 14644-1:2015 is an international standard that defines nine classes of cleanrooms, with class 1 being the highest and class 9 the lowest standard. The standard defines the number of particles per size allowed within one cubic metre of air. While many newer specifications refer to ISO 14644-1:2015 when specifying a manufacturing or packaging requirement, older drawings often refer to a US standard (US FED STD 209E) which was actually cancelled in 2001. To allow cross-referencing, table 1 below lists the equivalent of the older US standard in relation to the ISO standard.
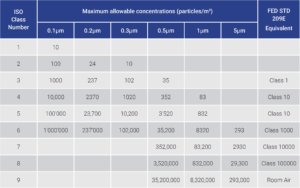
Most coating chambers are single door chambers, which means that are loaded and unloaded through the same door. This also requires the cleaning to be done from the room where the coating chamber is situated and loaded/unloaded.
The protective shields inside a coating chamber become coated during the normal production process and therefore require regular removal and cleaning. During the removal it is unavoidable for coating particles to flake off the shield surfaces and increase the dust contamination inside the coating department. Hence, care must be taken to avoid contamination of other parts of the department.
For this purpose, optics are cleaned and stored within the department in laminar flow cabinets. These are enclosed benches, where air is drawn in through a particle filter (generally situated above the bench or behind it) and blown towards the user in a smooth, laminar flow (vertical or horizontal, depending on type of cabinet).
Typically, laminar flow cabinets are available in cleanroom classes of ISO 4 or ISO 5. When operating laminar flow cabinets, it is important to follow the manufacturer’s requirements on maintenance. These usually ensure that the filter and air intake seals are regularly checked and that the filters are cleaned/changed at regular intervals to maintain the required cleanliness standard.
In practice, a critical interface is the process of loading the optics into the coating chamber prior to coating. During this process, the optics are removed from the laminar flow cabinet and positioned into their respective positions in the calotte within the coating chamber. To minimize the risk of dust settling on surface of the optics and then getting embedded in the coating during the coating process, it is important that particular care is being taken during this step. The optics need to be transported in an enclosed box and the surfaces protected by caps, which are only removed immediately prior to closing the coating chamber door and putting the chamber under vacuum.
During the cleaning of the optics, which will be covered in a separate technical note, it is important that the correct materials such as lint free cleaning tissue and chemically pure cleaning solvents are being used. A thorough inspection of a cleaned optic, usually under a bright halogen light against a black background, is also vital.
References
BS EN ISO 14644-1:2015, Cleanrooms and associated controlled environments, Classification of air cleanliness by particle concentration, ISBN 0 9267107062
Fabrication Methods For Precision Optics, H. H. Karow, Wiley Series in Pure and Applied Optics, John Wiley & Sons, Inc (1993)